About
Mel’s interest in 3D printing began when she realised that her job wasn’t for her. She wanted to do something that would help people and make the world a better place. So, she bought a 3D printer. She didn’t know how to use it. She didn’t know how it worked. But she knew she could learn.
After teaching herself how to 3D print, Mel opened up a community maker space called Makers Place in Leichhardt, Sydney. This is a place where people come and learn how to use 3D printers and other tools. At Makers Place, people can be creative and make their ideas a reality.
This is when Mel met Johan Du Plessis, a disability carer who is passionate about innovation in the disability sector.
Together, Mel and Johan hosted events called Make-a-thons, which paired people with accessibility needs with a maker who could use their skills to design and make devices. The maker worked one-on-one with the user, so that the device could be made quickly, cheaply, and be custom-made to suit the user.
Through this work, Mel realised the need for cheap, quickly made orthotics for people who need support to walk – like children with cerebral palsy. And so Mel and Johan formed the company now known as AbilityMade (originally called AbilityMate). They started out specialising in making ankle and foot orthotic devices.
AbilityMade uses a flashing camera to take pictures of the child’s foot. The pictures are combined to create a 3D scan. Then, they work with a medical specialist (known as an orthotist) to design the orthotic devices. Once designed, the devices are printed and ready in around 48 hours – much faster than the traditional process! Because of the speed and low cost of making these orthotic devices, the AbilityMade team calls them ‘Magic Shoes’.
Mel and Johan worked with a disability technology accelerator program called Remarkable. Remarkable provides expertise and mentors. Mel and Johan crowdfunded their idea with the help of ING Direct Dreamstarter. This platform supports community projects such as this one.
Why it's important
Traditional orthotics can take months, with long wait periods and production times. Because of this, orthotic devices are sometimes made up to 3 sizes too big, so that kids can grow into them. These traditional devices can cost up to $5,000, and kids can go through about 4 a year as they grow! But things are changing, thanks to AbilityMade’s 3D printing method. This innovative approach makes orthotic devices quickly and cheaply, helping kids get their orthotics sooner, and saving their parents money!
Now, Mel is using her skills in 3D printing and entrepreneurship to improve the lives of other people while she revolutionises the orthotics industry. The AbilityMade team is working to make this technology open source, so that anyone, anywhere, with a high-quality 3D printer can print medical-grade Magic Shoes for children. This will help kids get good-fitting orthotic devices sooner, so they can walk and live like other kids. It will also take the pressure off orthotists, doctors, and those who have to pay for orthotic devices.
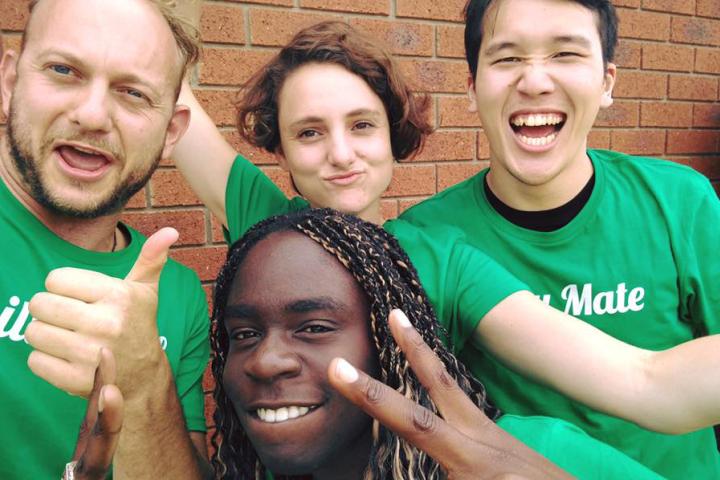
{Music playing in background]
Hi, my name is Mel Fuller and I’m a social entrepreneur who taught myself 3D printing so I could make the world a more accessible place.
I’m going to tell you a story about Daniel. He has cerebral palsy and he needs ankle and foot orthoses to help him walk and play, but these orthoses can take a really long time to make and by then his body shape and needs may have changed, they’re also really expensive.
I’m part of a team called Ability Mate and we’re working on a solution to Daniel’s problem.
By using 3D scanning technology, which is less invasive than traditional plaster cast and moulding methods, we’re prototyping and 3D printing these orthotics, which are cheaper and more accessible to everybody. In turn, making the lives of people like Daniel more inclusive. I taught myself the skills I needed to help my community and so can you.
[Enterprising Australians Logo]
[Image appears with Mel Fuller sitting in a workshop with 3D printers in the background]
[Image shifts to show Mel pick up an orthotic]
Kids who have physical disabilities sometimes have to wear ankle and foot orthotics for posture and mobility.
[Image shows orthotics next to a pair of children’s shoes]
These orthotics can cost anywhere between a thousand and five thousand dollars a pair.
[Image shifts to a parent assisting a child in getting orthotics on then socks]
A kid might need up to four or five pairs in a year because they’re growing. Currently, there’s a wait list of between four and nine months to see and orthotists to get these made.
[Image shifts to Mel pick up an orthotic]
Sometimes they make the orthotics three sizes too big so they can grow into them, but also sometimes the kids outgrow them, which causes secondary complications.
[Image shows a young child having their feet examined]
To make an ankle and foot orthotic, at the moment, is a very manual process. An orthotists takes a plaster cast of a child’s leg. With the plaster cast they mould it and then they fit it.
[Image shifts to Mel sitting in a workshop]
We’re working on a solution to that where we take a digital mould of a leg by using a 3-D scanner.
[Image shows a young child having their leg photographed next to a laptop showing a 3-D image of an orthotic]
With that digital mould it gets uploaded to a platform along with a prescription where it can be customised to the therapeutic need and to the shape of the kid’s leg and then we 3-D print it.
[Image shifts to an orthotic being made on a 3-D printer]
Improving the experience for the kid and making the orthotists time a lot more efficient.
[Image shifts to Mel holding an orthotic]
This is the 3-D printed ankle and foot orthotic for a two year old called Eve. She has to wear this when she wakes up until when she goes to bed. It took us many, many, many iterations to get to this point, but we moved pretty fast and we learnt really quickly what it was we should focus on. What else we’re doing this year is building, or developing a scanner that can take a quicker and better photograph of the kid’s leg.
[Image shifts to a young child having their leg photographed followed by a laptop showing a 3-D image of an orthotic]
At the moment we’re using handheld scanners so there’s a lot of room for error and fidgeting and stuff like that.
[Image shows the rig in a workshop]
So we’ll build the rig, we’re going to make it available in one Sydney clinic and then we’re going to open source everything. We’ll be developing a licence that encourages innovation on the product, but also keeps the kids safe.
[Image shifts to Mel sitting in the workshop]
Know what it is you’re working on and learn how to communicate it and practice that, because what that will come in handy for is being able to rally up supporters to get behind you and get behind your mission.